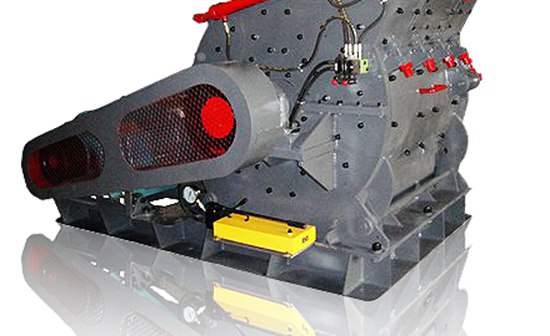
How does the residence time of materials in the mill affect the wet ultrafine pulverization process
The residence time of materials in the mill has a significant impact on the fineness and output of the product. Longer residence times generally result in finer product particle sizes but lower output. Conversely, shorter residence times can lead to coarser particle sizes and increased output. The choice of residence time should consider factors like slurry concentration, feeding speed, mill speed, and the degree of material dispersion.
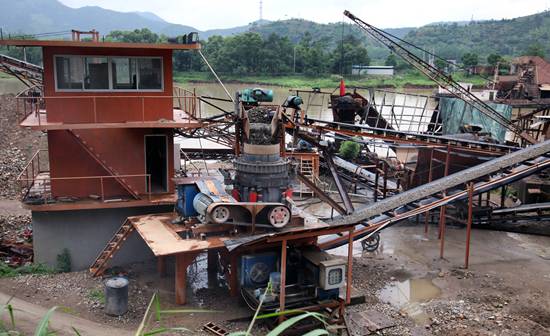
What role does the rotating speed of the mill play in the wet ultrafine pulverization process
The rotation speed or stirring speed of the mill plays a critical role in determining the fineness of the product, output, and energy utilization rate. Higher stirring speeds tend to increase the proportion of fine-grained materials in the product, but excessively high speeds can lead to reduced energy utilization. It's important to strike a balance to achieve optimal energy efficiency while maintaining the desired product quality.
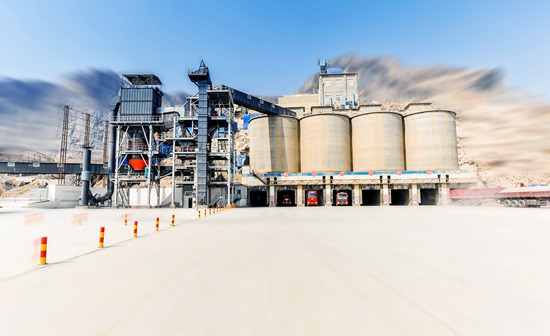
How does the density, diameter, and filling amount of the medium affect the wet ultrafine pulverization process
The density, diameter, and filling amount of the medium significantly impact the wet ultrafine pulverization process. The medium's density and particle size affect the product's particle size and the energy utilization rate of the mill. The choice of medium density and diameter should consider the material to be ground, feed size, slurry concentration, and mill speed. While increasing the filling amount within a certain range can enhance grinding strength, increase output, and fineness, excessive filling can lead to higher energy consumption and reduced energy utilization.
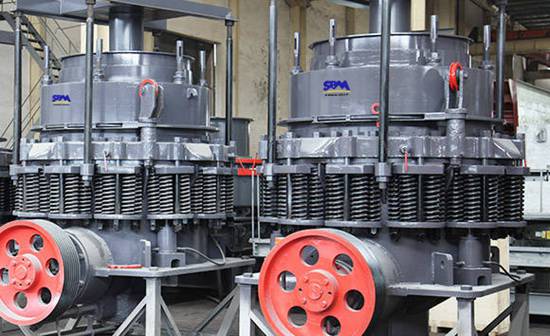
What are some of the equipment commonly used for wet ultrafine pulverization
In wet ultrafine pulverization, equipment such as stirring mills, sand mills, colloid mills, and high-pressure jet mills are commonly used. These machines are designed to achieve fine product particle sizes and narrow particle size distributions. The choice of equipment depends on the specific requirements of the material being processed and the desired end product quality.
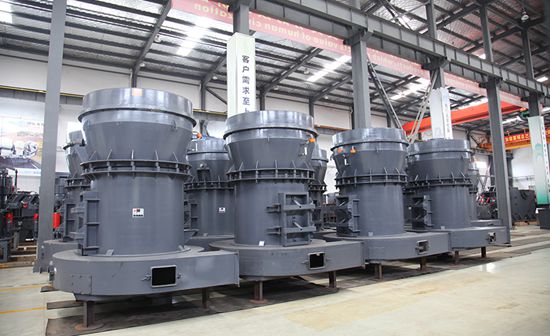
How do grinding aids or dispersants influence the wet ultrafine pulverization process
Grinding aids or dispersants play a vital role in wet ultrafine pulverization by reducing the strength of granular materials, lowering slurry viscosity, improving material dispersibility, and promoting slurry fluidity. They can increase product fineness, output, and reduce unit product energy consumption. However, their effectiveness is more pronounced at higher slurry concentrations. By adding a dispersant, the slurry concentration can be increased, leading to improved grinding efficiency.
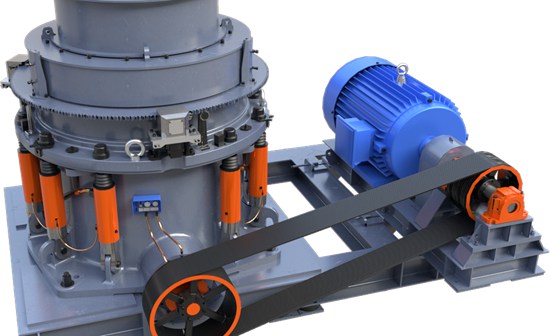
What materials are typically processed using wet stirring mills and sand mills for ultrafine grinding
Wet stirring mills and sand mills are commonly used to process a variety of materials, including calcium carbonate, kaolin (both soft and hard varieties), coal water slurry, mica, barite, gypsum, rare earth minerals, magnesium oxide, aluminum oxide, iron oxide, and magnetic materials. These processes can achieve micron and sub-micron level product fineness for a wide range of materials.
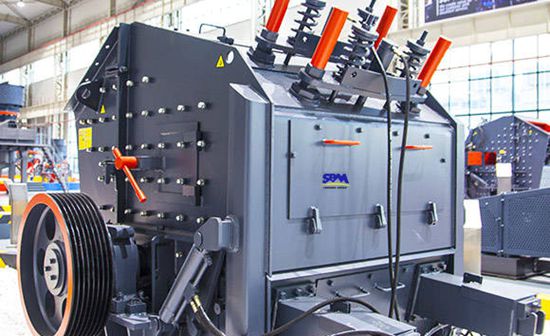
What are the advantages of wet ultrafine pulverization compared to dry processing
Wet ultrafine pulverization offers several advantages over dry processing. The presence of water acts as a grinding aid, making it easier to disperse the powder. Additionally, the higher density of water compared to air aids in fine classification. As a result, wet ultrafine pulverization is characterized by high crushing efficiency, fine product particle size, and a narrow particle size distribution. It is more energy-efficient than dry processing for ultrafine grinding operations.
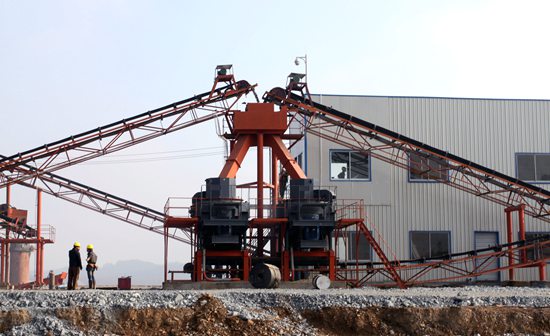
What are the different processes for ultrafine grinding using sand mills
Sand mills are typically used for wet grinding, and there are different processes for ultrafine grinding using sand mills. These processes can include:
- One machine with one tank: This process is relatively simple and suitable for applications where the product's particle size distribution is not strict.
- One machine with two tanks: This process is more complex but results in a more uniform product size.
- Three-machine series process: In this process, three sand mills connected in series use different speeds and grinding media to achieve a finer discharge particle size. This process shortens grinding time and improves efficiency but requires more equipment and space.

What are the key principles for process design and equipment selection in ultrafine pulverization
Process design and equipment selection in ultrafine pulverization should adhere to the following key principles:
- Meet the product guidelines: Ensure that the chosen process and equipment align with product quantity and quality requirements.
- Save investment: Minimize equipment investment while meeting product guidelines and performance requirements.
- Reduce energy consumption: Choose high-efficiency, low-energy-consumption equipment and simplify the process to minimize energy use.
- Reduce wear: Minimize equipment wear and grinding media consumption to lower production costs and maintain material purity.
- Meet environmental regulations: Comply with environmental protection laws and regulations to avoid legal issues and shutdowns.
- Ensure labor safety and health: Adhere to labor safety and hygiene regulations to create a safe and healthy working environment.
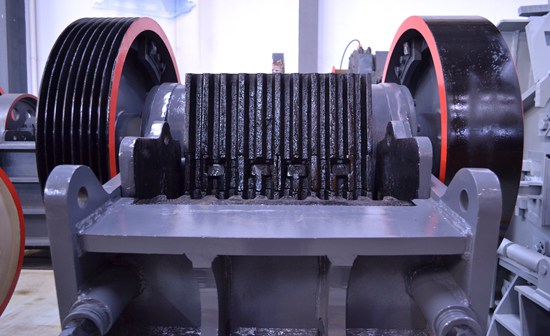
What is the significance of slurry concentration in the wet ultrafine pulverization process
Slurry concentration is a crucial process parameter that affects the effectiveness of wet ultrafine pulverization. Increasing slurry concentration can enhance the quantity of fine-grained materials and improve energy utilization. However, excessively high slurry concentration can lead to reduced pulverization efficiency, coarser product sizes, and decreased output. The ideal slurry concentration depends on factors such as medium properties, required product fineness, grinding aids, material types, and feed size.