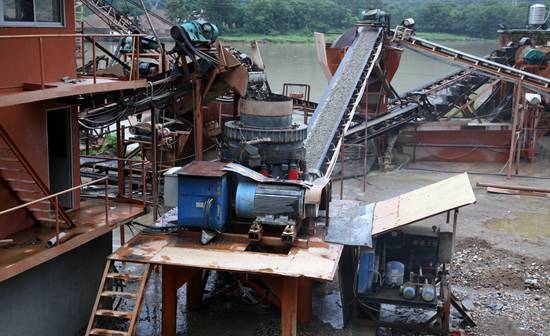
What are the different types of chalk micro powder mills offered by SBM, and how do they differ in terms of output and finished powder characteristics
SBM offers three types of chalk micro powder mills: HGM ultrafine grinding mill, CLUM vertical mill, and wet stirring mill. These mills vary in terms of their working principles, output, and the shape of the finished powder. HGM ultrafine grinding mill can produce powder ranging from 150 to 3000 meshes, CLUM vertical mill also covers the same range, while the wet stirring mill can produce finer powder between 325 and 6000 meshes. The differences in their working principles and features result in variations in the final product characteristics.
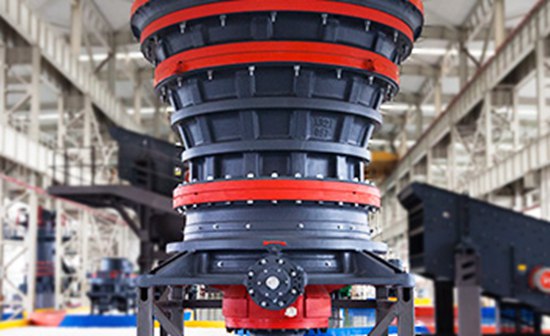
What is the role of the electromagnetic vibrating feeder and bucket elevator in the chalk powder production process
The electromagnetic vibrating feeder is responsible for evenly feeding chalk into the receiving device, ensuring a consistent supply of material for processing. It is characterized by its small size, lightweight design, low maintenance requirements, and minimal wear of the feeding trough.
The bucket elevator plays a crucial role in transporting chalk vertically to the equipment needed in the next step of the production process. It is known for its reliable operation, large conveying capacity, low maintenance needs, and minimal wear and tear on its components.
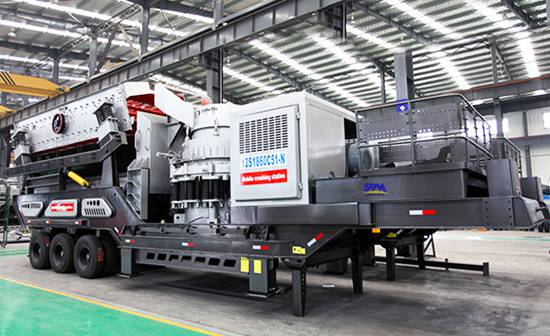
What are the key features and benefits of the HGM micro powder mill in chalk processing
The HGM micro powder mill has several key features and benefits:
- It offers a wide range of fineness options, from 150 to 3000 mesh.
- It has a newly designed grinding curve for improved efficiency.
- The mill has a high production capacity and reduced energy consumption.
- It includes a high-efficiency pulse dust collector to prevent dust pollution.
- The mill's working parameters can be precisely controlled for energy savings.
- It features a reversible structure and hydraulic adjustment for easy maintenance.
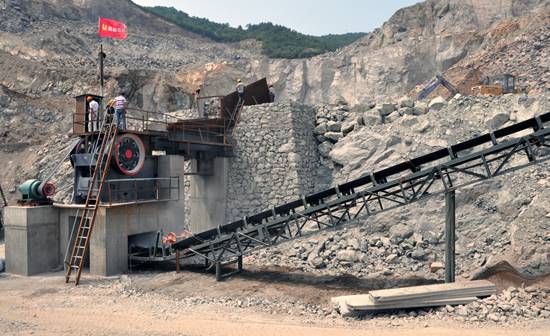
What are the main applications of chalk, and why is it important to process it into chalk powder
Chalk has various applications in industries like rubber, paper, paint, plastics, pigments, coatings, ceramics, sugar, casting, grease, and sealants. It is also commonly used in making white paint and chalk products. Processing chalk into chalk powder is essential to meet specific fineness requirements for these applications, as it enables better dispersion and coating ability, making it suitable for various industrial uses.
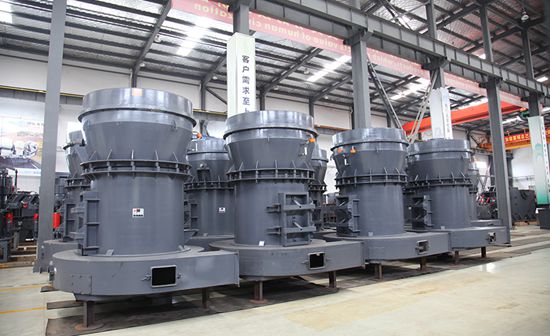
What is the chalk powder production process, and what equipment is involved in this process
The chalk powder production process consists of several stages:
- Crushing Stage: Large pieces of chalk material are crushed into smaller sizes to meet the feed material's fineness requirements.
- Grinding Stage: Small chalk pieces that meet the conditions for milling are fed into the grinding chamber, where they are pulverized.
- Classification Stage: The ground material is classified by a classifier, separating the unqualified powder for re-grinding.
- Powder Collection Stage: The fine powder that meets the required fineness enters the powder collection system, where the finished product is separated from the gas and collected in a silo for packaging.
The equipment used in this process includes jaw crushers, bucket elevators, storage bins, vibrating feeders, micro powder mills, powder classifiers, powder collectors, pulse dust collectors, high-pressure fans, and electrical control systems.
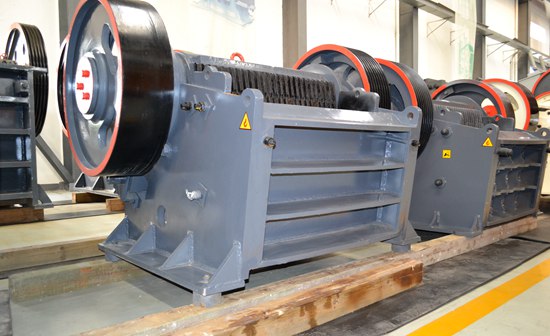
How does SBM's chalk micro powder mill contribute to energy efficiency and environmental protection in the chalk processing industry
SBM's chalk micro powder mill offers several features that contribute to energy efficiency and environmental protection:
- The mill's grinding curve design enhances grinding efficiency, resulting in a 40% higher production capacity compared to other mills.
- Energy consumption is reduced by 30% compared to jet mills, making it more energy-efficient.
- The high-efficiency pulse dust collector prevents dust pollution during operation.
- Precise control of working parameters, such as grinding pressure and speed, further reduces energy consumption.
These features make SBM's chalk micro powder mill an environmentally friendly and energy-efficient choice for the chalk processing industry.
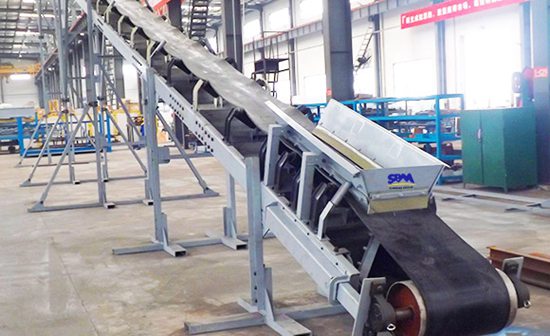
What are the characteristics of the wet stirring mill, and why is it suitable for producing ultrafine chalk powder
The wet stirring mill is ideal for producing ultrafine chalk powder with the following characteristics:
- It can produce ultrafine powders as fine as 2 microns with a 90% content in one milling operation.
- It has a large output, high efficiency, and low energy consumption.
- The temperature of the finished products remains low, ensuring good liquidity.
- It features a compact structure, ease of operation, and optional automatic control.
These attributes make the wet stirring mill a suitable choice for producing ultrafine chalk powder with high quality and efficiency.