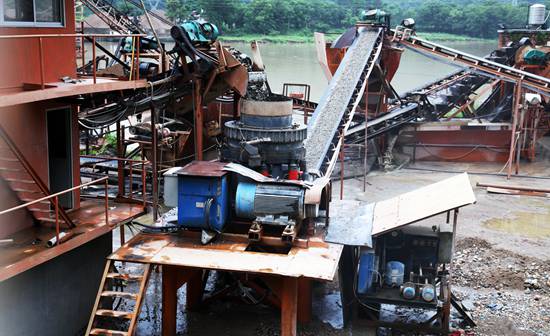
What is the significance of the unique roller shell and liner grinding curve in SBM's industrial powder grinder for quartz powder production
The unique roller shell and liner grinding curve in SBM's industrial powder grinder play a significant role in enhancing the efficiency and quality of quartz powder production. This feature allows for:
- Improved working efficiency of the mill, resulting in a higher production capacity.
- Enhanced whiteness and cleanliness of the finished product, making it more suitable for various applications.
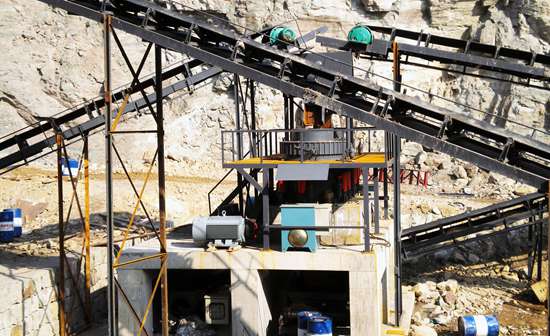
What is the difference between quartz sand and quartz powder, and how are they produced
Quartz sand and quartz powder are both derived from quartz ore, but they differ in terms of fineness and application. Quartz sand, with a fineness of less than 120 mesh, is typically used in various industrial applications. In contrast, quartz powder, or refined quartz sand, has a fineness exceeding 120 mesh and is processed through multiple stages, including crushing, sorting, cleaning, acid treatment, high-temperature melting, medium crushing, fine grinding, grading, and iron removal. These processes result in different specifications of quartz powder, such as 150mesh, 200mesh, 325mesh, 400mesh, 600mesh, 1500mesh, and 2000mesh.
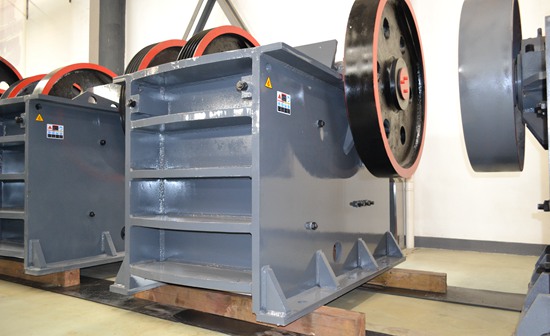
How does SBM's industrial powder grinder offer benefits in terms of energy efficiency and operational stability for quartz powder production
SBM's industrial powder grinder is designed to be energy-efficient and operationally stable. Some key advantages in this regard include:
- Energy consumption reduced by 30%-50% compared to ordinary mills.
- The use of electronic limit technology and mechanical limit protection to avoid destructive impacts due to machine vibration, ensuring stable operation.
- A reversible structure and hydraulic adjustment system, allowing quick and easy maintenance operations, reducing downtime losses.
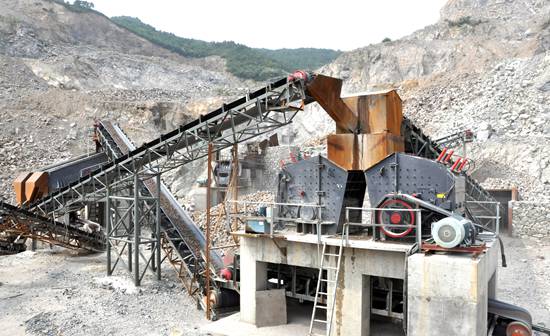
What are the advantages of using an ultra-fine wet stirring mill for producing high-fineness quartz powder (3000+ mesh)
For the production of extremely high-fineness quartz powder exceeding 3000 mesh, an ultra-fine wet stirring mill is recommended. This mill offers several advantages:
- The ability to produce ultrafine powders with a content of 90% at 2 microns in a single milling operation.
- High output and efficiency, along with low energy consumption and environmental friendliness.
- A vertical-shaped star wheel reducer for higher transmission efficiency and smoother operation.
- Low consumption of grinding media, which reduces pollution, and lower finished product temperatures for better liquidity.
- Compact structure, ease of operation and maintenance, and optional automatic control.
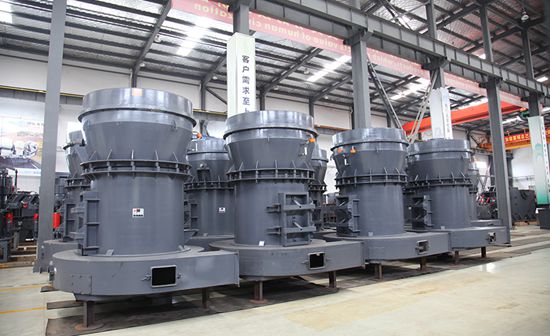
What are the main applications of quartz powder in various industries, and what role does its fineness play in these applications
Quartz powder finds applications in a variety of industries, including ceramics, enamel production, precision modeling, chemicals, coatings, building materials, metallurgy, high-quality glass manufacturing, metal rust removal, polishing, water treatment, and more. The fineness of quartz powder is crucial in these applications. For instance, in ceramics and precision modeling, finer quartz powder with a high mesh size is often preferred for its ability to enhance product quality and appearance. In contrast, coarser quartz powder may be used in applications like metal rust removal, where its abrasive properties are essential.
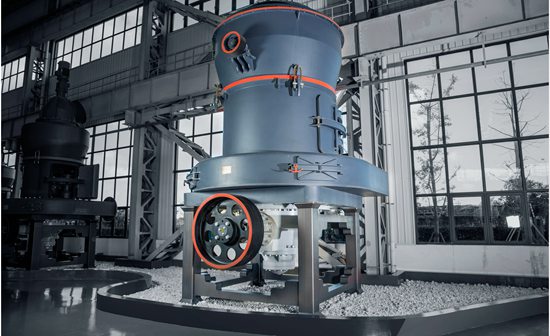
Can you provide a specific case study where SBM's industrial powder grinder was used for quartz powder production
One specific case study involves a customer in Saudi Arabia who required the production of 600 mesh quartz stone powder with an hourly output of more than 10 tons. SBM recommended the use of their industrial powder grinder for this application. The grinder offered the following benefits:
- Higher capacity and better powder quality.
- Improved overall performance with reduced energy consumption.
- Enhanced whiteness and cleanliness of the finished product, meeting the customer's specific requirements.
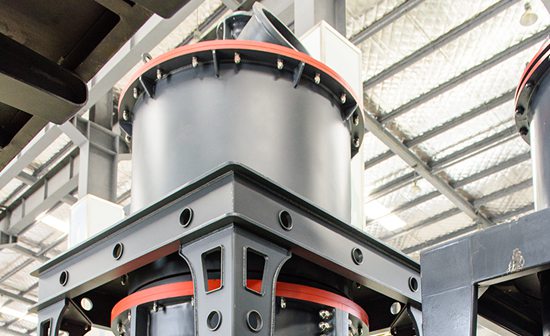
What is the typical production process for quartz sand and quartz powder
The production process for quartz sand involves several stages, including crushing, screening, and cleaning, while quartz powder production involves additional steps for fine grinding, grading, purification, powder collection, and noise reduction. The key stages for quartz sand and quartz powder production include a silo, vibrating feeder, jaw crusher (for sand), bucket elevator, electromagnetic vibrating feeder, and the industrial powder grinder. The specific milling equipment used depends on the desired fineness of the final product.
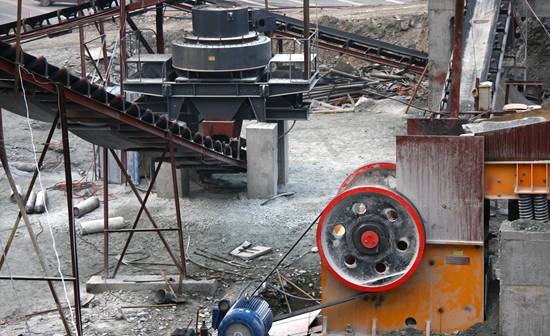
How can the newly developed HGM and CLUM industrial powder grinders benefit quartz powder production
The HGM and CLUM industrial powder grinders, developed and produced by SBM, offer significant advantages for quartz powder production. These grinders can produce quartz powder with a wide range of fineness, from 150 to 3000 mesh, and the fineness is adjustable. Some key benefits include:
- Higher production capacity compared to jet mills and stirring mills, with a 40% increase in production.
- Lower energy consumption, with only 30% of the energy consumption of jet mills.
- Precise control of grinding parameters through a PLC control system and multi-head powder selection technology.
- No dust pollution during operation due to a high-efficiency pulse dust collector and noise reduction features.
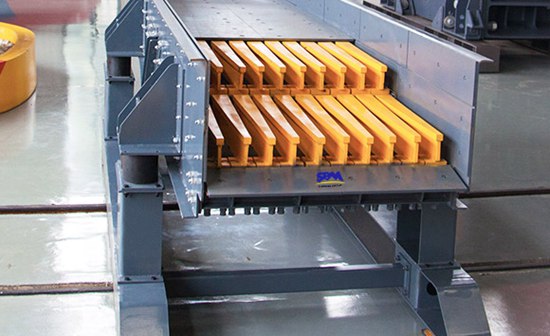
What is the main purpose of quartz powder (refined quartz sand) in various industries
Quartz powder, also known as refined quartz sand, serves as a crucial raw material and auxiliary material in several industries. It is used in ceramics, enamel production, precision modeling, chemicals, coatings, building materials, metallurgy, high-quality glass manufacturing, metal rust removal, polishing, water treatment, and more. Its unique properties, including high purity, white color, and hardness, make it versatile for a wide range of applications in these sectors.