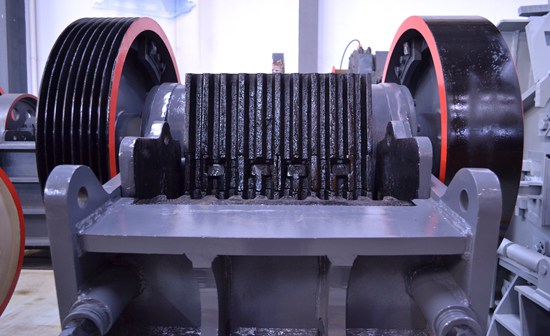
How can manufacturers select the most suitable mill for bentonite processing
Manufacturers should consider the following factors when selecting a mill for bentonite processing:
- Production requirements
- Available budget
- End-product specifications
- Downstream industry demands
- Environmental considerations
Choosing the most appropriate mill ensures cost-effectiveness and optimal performance for bentonite processing.
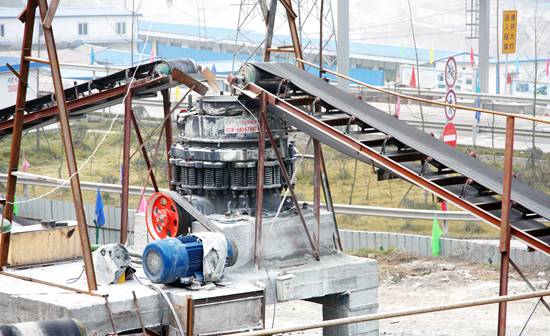
What are the stages involved in the production of bentonite powder
The production of bentonite powder involves several stages:
- Socialization stage: Most natural bentonite is calcium-based, and this stage involves transforming it into sodium-based bentonite for better performance.
- Drying stage: Sodiumized bentonite typically has higher moisture content, so it is dried to reduce moisture levels.
- Grinding stage: Dried bentonite is crushed and ground to the desired fineness for further processing.
- Classification stage: The ground bentonite is classified, and the unqualified powder is returned for regrinding.
- Powder collection stage: The final powder, meeting the required fineness, is separated from the gas and collected for packaging.
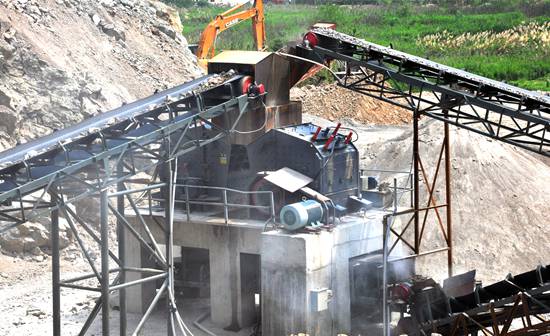
What is the significance of the grinding stage in bentonite production
The grinding stage is a crucial step in bentonite production. It involves reducing the bentonite to the desired fineness for different industrial applications. The type of grinding mill used can impact the final product's properties and applications. Bentonite can be ground into ultrafine powder with fineness up to 3000 mesh, making it suitable for diverse industries.
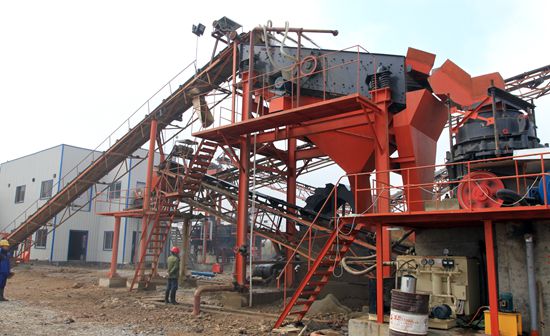
What are the advantages of using the HGM and CLUM series ultrafine mills in bentonite processing
The HGM and CLUM series ultrafine mills are popular choices for grinding bentonite due to their specific advantages:
- HGM Series: These mills offer a small footprint, simple operation, stable operation, long service life, high efficiency, energy savings, and environmental friendliness. They are suitable for various industrial applications with a moderate budget.
- CLUM Series: These vertical mills provide a larger output, higher fine powder content, and a better powder shape. They are ideal for industries with high-end requirements, such as papermaking and coatings.
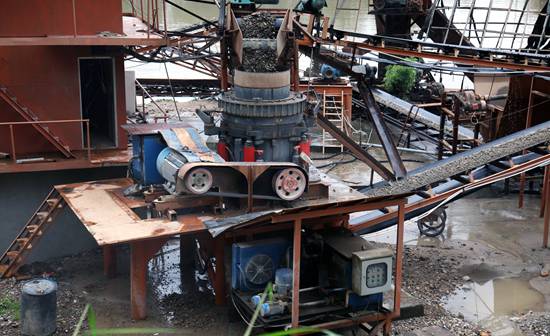
What are some specific applications of modified sodium bentonite
Modified sodium bentonite is used in various applications based on its properties:
- Drilling: It improves the production capacity in high-temperature and high-pressure furnaces.
- Foundry: In wet mold casting, it enhances the smoothness of casting surfaces.
- Papermaking: It acts as a filler to improve paper brightness.
- Textile industry: Sodium bentonite's adhesion and suspension properties make it suitable as an antistatic coating, replacing starch as a coating.

What are some of the applications of bentonite in different fineness levels
Bentonite is used in various industries at different fineness levels:
- Below 200 mesh: Bentonite can be used as a feed additive, particularly in the agriculture and light industry sectors.
- 200-325 mesh: This fineness level is suitable for applications like drilling mud, flame retardants, and as a paper filler to improve coating properties.
- Above 325 mesh: Bentonite's high fineness makes it effective for purifying cooking oil, gasoline, and kerosene, as well as in wastewater treatment.
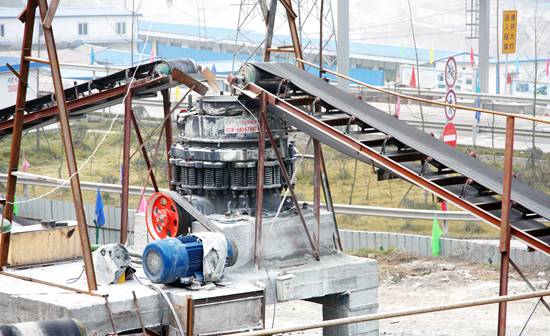
What are the key properties and uses of bentonite
Bentonite is a natural mineral material known for its strong hygroscopicity, expansibility, and cation exchange capacity. It has various applications, such as purifying and decolorizing agents, binders, thixotropic agents, and more. It finds uses in agriculture, light industry, cosmetics, and medicine. Bentonite can also be processed into different fineness levels for various industrial applications, including agriculture, papermaking, and drilling.
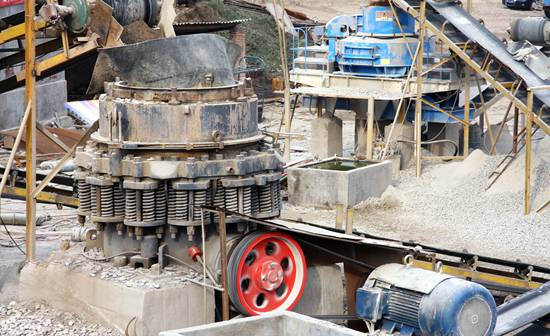
What is the difference between calcium-based and sodium-based bentonite
The primary difference lies in their performance. Calcium-based bentonite, which is more commonly found in nature, generally has inferior properties compared to sodium-based bentonite. Sodium-based bentonite is preferred due to its superior properties, including better moisture content and cation exchange capacity, making it more versatile for various industrial applications.