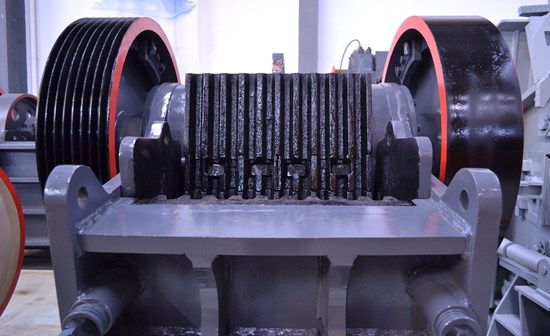
What are the advantages and characteristics of talc, and how is it used in different industries
Talc has several advantages, including insulation, acid resistance, a high melting point, good gloss, strong adsorption, and anti-sticking properties. Talc powder obtained from the talcum powder making machine is white, odorless, tasteless, non-toxic, and environmentally friendly. It finds applications in the chemical, ceramics, cosmetics, medicine, paper making, and electric porcelain industries due to its unique properties.

What are some of the notable features of a talcum powder mill production line
A talcum powder mill production line offers several advantages, including:
1. Efficient Dust Removal: The production line is equipped with dust removal equipment, achieving low dust emission and a dust-free workshop environment.
2. Stability and Low Vibration: The production line runs stably with reduced vibration and lower operating noise.
3. Automatic Control System: It features remote control for convenient operation and maintenance.
4. Compact Design: The equipment is more compact, reducing the production line's area and investment cost.
5. High Powder Extraction Rate: The finished talc powder has high quality and purity, with a sieving rate exceeding 99.99%.
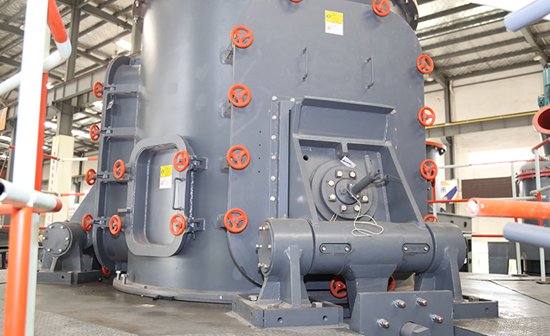
What are some of the materials that can be processed using the talcum powder making machine
The talcum powder making machine is versatile and can process various materials, including non-metallic ores, shells, bamboo, and coconut shells. This versatility makes it suitable for a variety of applications.
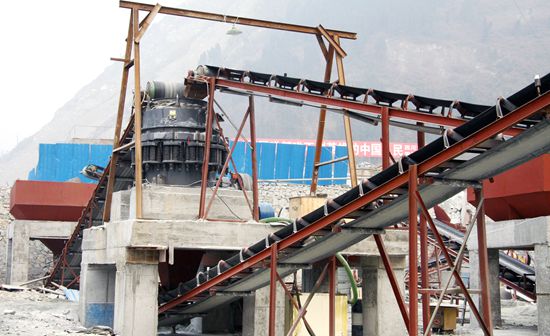
What is the purpose of a talcum powder making machine, and what are its key features
A talcum powder making machine, such as the HGM ultrafine grinding mill, is used to produce talcum powder and other non-metallic ore powders. It can also process hard calcium-containing materials like shells and coconut shells. The key features of this machine include stable operation, simple operation, convenient maintenance, high efficiency, and environmental friendliness. One notable advantage is that it allows for 24-hour operation without downtime.
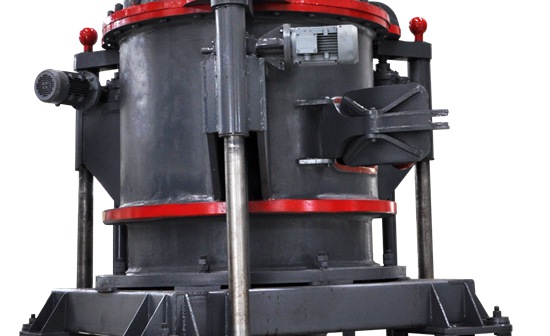
What are the four types of talc powder processing, and how do they differ
Talc powder processing can be categorized into four types:
1. Coarse talc powder processing (0-3MM)
2. Fine powder processing (20 mesh-400 mesh)
3. Ultra-fine powder deep processing (400 mesh-1250 mesh)
4. Micro-powder processing (1250 mesh-3250 mesh)
These categories differ in terms of particle size and intended use, with each requiring specific processing techniques.
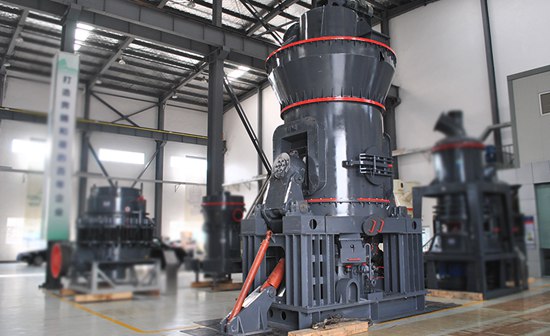
Can you describe the key stages in the process flow of a talcum powder production line
A talcum powder production line typically consists of two main stages: crushing and grinding. The process flow includes the following steps:1. Crushing: Talc material is crushed by a crusher to a fineness suitable for milling (10mm-50mm).
2. Milling: Crushed talc is sent to a silo, then to the mill's grinding chamber through a vibrating feeder for further processing.
3. Classification: Ground material is classified by a classifier, and any unqualified powder is sent back for re-grinding.
4. Collecting Powder: The finished powder is collected through a dust collector and sent to a storage silo for packaging.
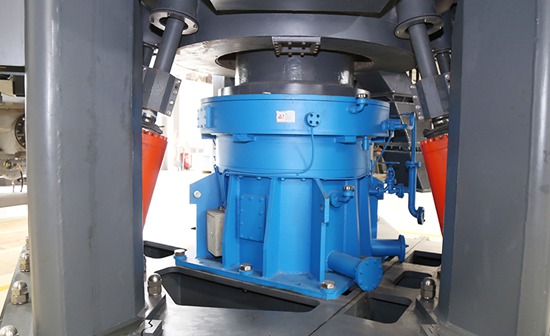
What are the adjustable fineness and capacity of the talcum powder making machine
The talcum powder making machine offers an adjustable fineness range of 150-3000 mesh and a capacity ranging from 0.5 to 45 tons per hour. This flexibility allows it to cater to a wide range of production requirements.
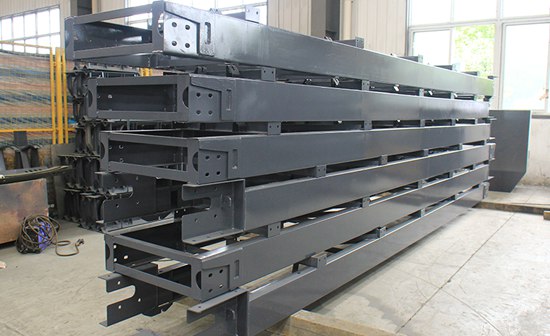
What are the core processing equipment options for talcum powder making, and how do they differ
There are several core processing equipment options for talcum powder making, each suited to different processing needs:
- Talcum Powder Making Machine (HGM ultrafine grinding mill)
- Vertical Roller Mill (CLUM ultrafine vertical roller mill)
- High-Pressure Mill (High-pressure mill)
These equipment choices are based on the desired fineness and the type of talc powder being produced.