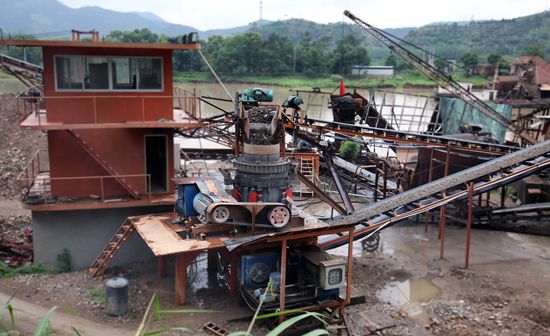
What are the advantages of using a high-pressure grinding mill compared to traditional pulverizers like Raymond mills and ball mills
High-pressure grinding mills offer several advantages over traditional pulverizers:
1. Enhanced Grinding Force: The use of a high-pressure spring device increases the grinding force of each grinding roller assembly, improving milling efficiency significantly.
2. Larger Grinding Area: The grinding height of the grinding roller and grinding ring is increased, providing a larger grinding area for more efficient material processing.
3. Greater Shovel Capacity: The machine is designed with a large shovel, allowing for more efficient material feeding.
4. High Classification Accuracy: It offers precise classification of materials, ensuring high-quality finished products.
5. Double Cyclone Collector: The double cyclone collector efficiently collects fine particles, enhancing the dust collection process.
6. Low Noise and Stable Operation: The main engine is equipped with a buffer device, and the casing structure is optimized for noise reduction, resulting in stable and quiet operation.
7. Quick Maintenance: The main engine and analysis machine feature quick-change pressing devices, making maintenance convenient.
8. Dust Pollution Control: Residual air is collected by cloth bags, ensuring there is no dust pollution during operation.
9. Improved Pneumatic Conveying: The high-pressure centrifugal fan in the blower enhances pneumatic conveying capacity.
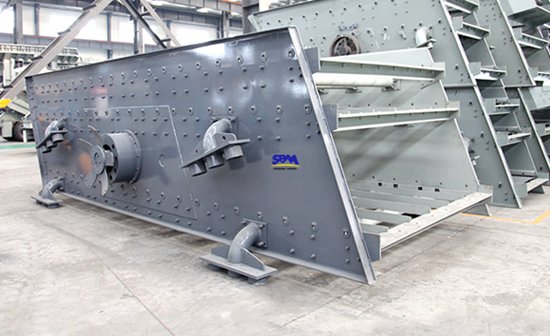
What types of materials can be processed using a high-pressure grinding mill, and what is the range of finished product fineness
A high-pressure grinding mill is versatile and can process more than 280 different materials from various industries, including mining, metallurgy, chemical, and building materials. Some of the applicable materials include quartz, feldspar, calcite, limestone, talc, marble, granite, dolomite, bauxite, iron ore, phosphate rock, ceramics, slag, barite, bentonite, and coal-related materials. The machine is designed to grind non-flammable and non-explosive materials with a Mohs hardness not exceeding 9.3 and a humidity level below 6%. The finished product's fineness can range from 80 to 600 mesh, making it suitable for a wide variety of industrial applications.
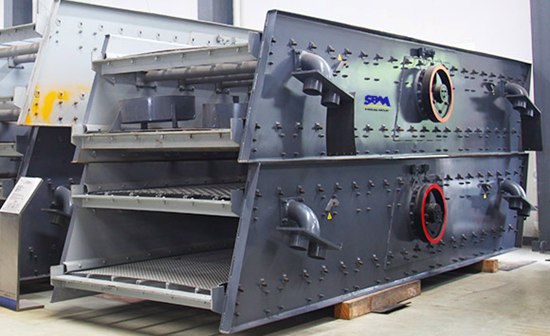
What is the structure of a high-pressure roller mill, and how does it work
The high-pressure roller mill consists of the main engine, blower, ultra-fineness analyzer, finished cyclone powder collector, bag filter, and connecting air duct pipes. In its grinding chamber, the grinding roller assembly is suspended on the grinding roller hanger via the cross-arm shaft. A high-pressure spring device applies pressure to the grinding roller, ensuring it tightly presses against the inner surface of the grinding ring.
When the motor is in operation, the blade on the blade holder rotates in sync with the grinding roller. The grinding rollers rotate on themselves while rolling on the inner circular surface of the grinding ring. The speed adjustment of the analysis machine determines the fineness of the powder.
As material enters the grinding chamber, it's scooped up by a shovel and sent for grinding. The crushed powder is brought into the analyzer with the blower's circulating air. Qualified fine powder enters the cyclone powder collector with the airflow, while larger particles return to the grinding chamber for regrinding. The remaining air enters the bag filter for purification. The length of the high-pressure spring is adjusted to maintain a constant grinding pressure between the grinding roller and the grinding ring, ensuring stable output and fineness.
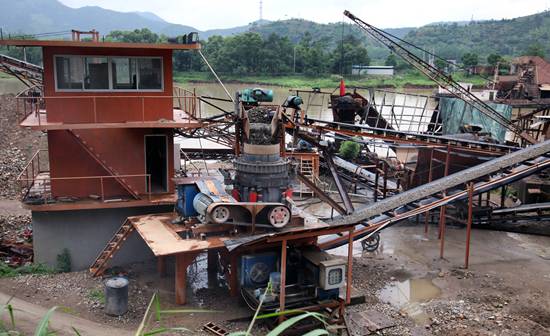
What are the performance characteristics of a high-pressure grinding mill
High-pressure grinding mills offer several performance characteristics:
1. Broad Application Range: These mills can handle a wide variety of materials, making them suitable for various industries.
2. Increased Grinding Force: The high-pressure spring increases the grinding force on the material, resulting in more efficient grinding.
3. Energy Efficiency: Compared to jet mills, high-pressure micro-powder mills have lower energy consumption, making them more energy-efficient.
4. Cost-Effective: These mills are cost-effective, with a lower price compared to other similar mills while offering similar output and fineness.
5. Excellent Sealing: The grinding device features overlapping multi-stage sealing, providing good sealing performance, no dust or noise problems, and making it an environmentally friendly choice.
6. High Automation and Easy Maintenance: These mills have a relatively high degree of automation, making them easy to operate, disassemble, and maintain.
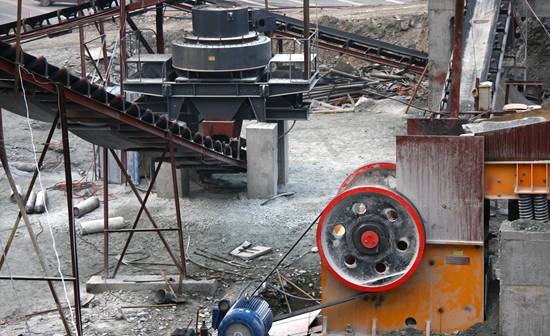
What are the main components of a high-pressure grinding mill, and how do they contribute to its functionality
A high-pressure grinding mill consists of several key components, including the main engine, reducer, analyzer, pipeline device, blower, dust collector, jaw crusher, bucket elevator, electromagnetic vibrating feeder, and electric control system. These components work together to grind a wide range of materials efficiently. The main engine, with its innovative features like parallel working surfaces and roller linkage pressurization, overcomes the limitations of traditional industrial pulverizers in terms of application range, output, fineness, energy consumption, and service life. This makes it an ideal substitute for traditional Raymond mills and ball mills, offering various advantages in material processing.